制造PVC芯层发泡管材有三种工艺路线。
1.单机挤出法
所谓单机挤出法就是由一台大功率的双螺杆挤出机挤出发泡塑料,精确控制其内外皮层的温度,使其低于发泡温度而结皮。这种一步法生产PVC芯层发泡复合管的工艺,内层温度很难控制,机头模具构造复杂,制造费用昂贵;同时大量的发泡剂被作为填料使用,提高了生产成本。因此,目前采用单机挤出法生产PVC芯层发泡复合管材的应用范围很狭窄。
单机挤出法生产PVC芯层发泡复合管的工艺流程为:
树脂1
助剂高速热混-.冷混一挤出一发泡呻冷却定型
发泡剂J
牵引-定长切割一翻转堆积一检验一成品入库
2.双机挤出法
双机共挤法,是目前生产PVC芯层发泡复合管最广泛采用的一种方法。即采用二台挤出机来生产PVC芯层发泡复合管,其中一台挤出机挤出PVC不发泡混合料,在配料模头中将料流分成两股,这两股熔融的料流形成管材的内外皮层;另一台挤出机将发泡PVC混合料挤人到同一配料模头中,处于内外层的中间,即为中间发泡芯层。通过调整两层塑料的品种或配方,可以使制品达到所需要的密度和尺寸。另外,制品内外表层虽然工艺配方相同,但通过控制内外层不同的冷却速率,可获得不同的硬度。
双机共挤芯层发泡复合PVC管材的生产工艺流程为:
树脂
皮层; 一高速热混.冷混.定量加料.挤出
助剂
—+
树 №
芯层:发泡 一高速热混.冷混.定量加料一挤出
其他助
共挤发泡机头一真空冷却定径-- -次喷淋冷却一-牵引一
定长切割一翻转堆积-扩口.成品
在生产过程中,皮层原料和芯层原料必须严格分开,分别进行高速热混、冷混,加料及挤出过程不得发生掺混现象。分别挤出的皮层及层料同时经过具有特殊结构的机头模具,形成致密均匀的发泡中间芯
层和坚硬密实的皮层,其余生产过程与普通实壁PVC管材的生产过程
相同。
3.三机共挤法
图7-2为三机共挤法生产芯层发泡复合管生产过程示意图。三机共挤法与双机共挤法都属于共挤塑法,是由三台小型的单螺杆挤出机,或一台双螺杆挤出机和两台单螺杆挤出机挤出较大口径的管材,其内层、外层和芯层均由独立的挤出机挤出。这样发泡芯层和管内层就不必使用Tio2,节约了原料成本。芯层还可挤出回收的废料而成填充管,并可根据管材的特殊使用环境来独立地设计内外皮层的配方,如内层可设计为具有高抗腐蚀和高光滑性能,外层可设计为具有抗紫外线及耐老化等性能。在独立配方设计方面,三机共挤法优于单机挤出法与双机共挤法,因此,很有发展前景。
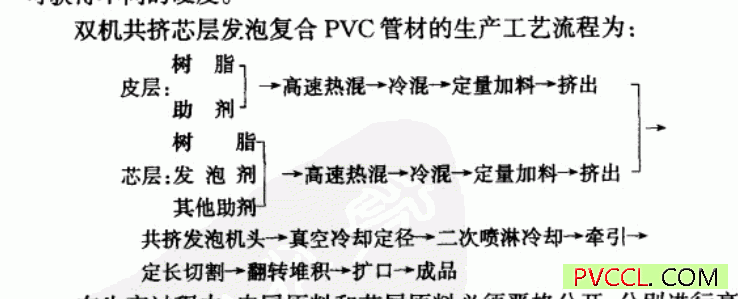
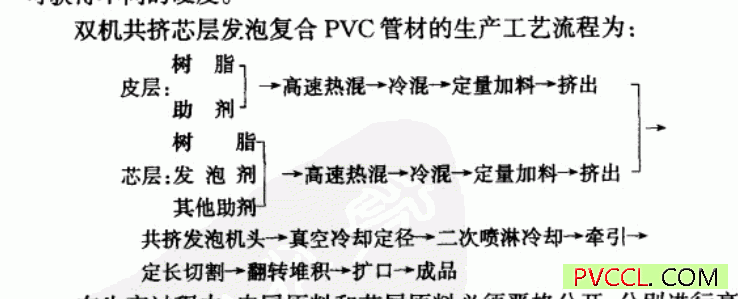
三机共挤法生产PVC芯层发泡复合管的工艺流程为:
树脂
外层: +高速热混.冷混.挤出
助剂
树 置
芯层:发泡舅 .高速热混一冷混一挤出
其他助;1
内层::嘉].高速热混一冷混一挤出
一三层共挤发泡机头
一真空冷却定型一二次喷淋冷却一牵引一定长切割一
翻转堆积.扩口一成品
在生产过程中,必须把皮层与芯层原料严格区分,将它们分别进行配料、高混、冷混、上料和挤出,木得发生掺混现象。有特殊要求的,内层和外层也可单独配料。分别挤出的皮层及芯层料同时经过具有特殊结构的配料模头,从而形成泡孔均匀的发泡芯层和坚硬密实的皮层,然后经定型、牵引、切割,最后得到芯层发泡复合管材。